Construção de paredes de concreto e suas tipologias. 4. Vários métodos de concretagem
EM construção moderna, na construção de novos edifícios, um dos tipos de paredes mais populares a serem erguidos é o muro de concreto, devido à acessibilidade financeira e rapidez de construção deste tipo. As paredes de concreto consistem em blocos especiais. Eles são obtidos misturando vários tipos de cargas com ligantes e depois despejando essa massa de concreto em formas especiais.
Dependendo dos materiais utilizados, os blocos de concreto para paredes vêm em diferentes tipos:
- blocos de concreto;
- blocos de concreto celular;
- espuma de concreto;
- concreto de argila expandida;
- poliestireno expandido;
É claro que todos esses tipos de blocos de concreto utilizados na construção de paredes possuem certas características que dependem diretamente das matérias-primas utilizadas.
Um dos materiais de construção mais comuns é o bloco de concreto, no qual diversas escórias metalúrgicas e combustíveis de diversos tamanhos de grãos com adição de areia podem ser utilizadas como carga. A resistência da escória resultante depende da porcentagem de escória grande e pequena no bloco de concreto. material de construção. Quanto mais escória fina na composição, mais resistentes serão os blocos de concreto. Blocos de concreto celular para construção de paredes são obtidos pela mistura materiais necessários em uma autoclave.
As paredes construídas com esses blocos possuem alto isolamento térmico e baixo peso, o que pode reduzir significativamente a carga sobre a fundação.
Os blocos de espuma de concreto geralmente são feitos diretamente no canteiro de obras, sem o uso de autoclave. Este tipo de blocos pode ser facilmente processado, o que permite erguer edifícios das mais complexas estruturas.
O concreto de argila expandida é altamente durável e muito difícil de processar, por isso é mais frequentemente usado no vazamento de um monólito.
Os blocos de poliestireno expandido são feitos misturando cimento e grânulos de poliestireno expandido. Esses blocos se diferenciam pela leveza, resistência, alto isolamento térmico e baixo coeficiente de absorção de umidade.
Corte de paredes de concreto de alta qualidade de várias maneiras
Muitas vezes durante a remodelação ou execução revisão há necessidade de fazer uma nova porta ou janela abrindo parede monolítica, faça furos ou faça estrias. Para resolver todos esses problemas, utiliza-se o corte paredes de concreto.
Existem várias maneiras de cortar paredes de concreto acabadas:
- corte com martelo perfurador;
- corte combinado;
- corte diamantado de paredes de concreto;
- corte de corda.
Na maioria das vezes, o corte de concreto é feito com equipamentos de construção especiais, usando rodas diamantadas, ou seja, É realizado o corte de diamante de paredes de concreto acabadas. Se houver necessidade de cortar concreto em uma profundidade rasa, para isso você pode usar uma rebarbadora com um disco diamantado instalado. Este processo é acompanhado pela liberação de grande quantidade de poeira, portanto, recomenda-se regar periodicamente o local do corte e o próprio disco diamantado.
Antes de iniciar os trabalhos de corte de concreto, é necessário estabelecer a composição qualitativa da superfície a ser tratada e determinar a presença de uma armadura. E com base na composição estrutural, a marca do disco diamantado de corte é selecionada. Ao cortar paredes de concreto, é imprescindível o uso de proteção respiratória e de mucosas.
Observe que às vezes você pode encontrar algo como corte a laser de paredes de concreto. Porém, hoje não existe uma única empresa que ofereça corte de paredes de concreto com laser. Na maioria das vezes, esse serviço nada mais é do que corte de diamante em paredes de concreto.
Se necessário, as paredes de concreto podem ser submetidas a processamento mecânico, o que permite não limitar as possibilidades de projeto na realização de grandes reparos. Para o mais acessível e maneiras eficazes O corte de concreto refere-se ao corte com lâminas diamantadas.
O isolamento adequado das paredes externas de concreto melhora a economia de energia
Na construção de edifícios de concreto, uma das etapas importantes da construção é o isolamento externo das paredes de concreto. Afinal, o isolamento permite reter significativamente o calor no interior da casa, o que garante poupanças significativas de energia. Para que o isolamento externo das paredes de concreto dos edifícios desempenhe suas funções de forma eficaz, é necessário cumprir rigorosamente todos recursos tecnológicos Este processo.
A seguir, sugerimos considerar como isolar você mesmo uma parede de concreto do exterior. Antes de proceder ao isolamento, deve-se limpar bem a superfície da parede, remover todas as irregularidades e aplicar um primer para evitar a absorção de umidade durante o funcionamento da edificação. Depois disso você precisa instalar perfil de rodapé, cuja espessura está diretamente relacionada à espessura do isolamento. Depois disso, você pode iniciar o processo de colagem do isolamento.
A cola pode ser aplicada no centro e nas bordas do painel isolante, o que permite economizar solução adesiva. As lajes são fixadas adicionalmente com buchas na proporção de 5 buchas por metro quadrado. Após a secagem completa, uma malha especial reforçada é fixada ao isolamento para fortalecer toda a estrutura. Outra camada de cola é aplicada no topo da malha. Após a secagem da cola, pode-se aplicar uma camada final decorativa, que pode ser feita com o máximo vários materiais. Além disso, além da função estética, a camada decorativa também possui uma carga funcional de conservação de calor.
Em princípio, quase todo mundo sabe, em termos gerais, como isolar de forma independente uma parede de concreto fora de uma casa: muito já foi escrito sobre isso. O principal nesse processo é acompanhar as etapas da obra, escolher materiais de qualidade e não ter pressa na finalização da obra.
As paredes de concreto podem, e o mais importante, precisam ser isoladas, conseguindo a conservação do calor interno nas instalações com baixos custos de energia. E, além disso, o processo de isolamento externo das paredes de concreto aumentará significativamente a vida útil da edificação, devido à proteção de alta qualidade das paredes contra os efeitos da precipitação e das mudanças de temperatura.
Uma etapa importante da construção é a impermeabilização das paredes de concreto da casa
Ao construir um edifício com blocos de concreto, atenção especial deve ser dada a um processo como a impermeabilização de paredes de concreto. Esta etapa da construção não pode ser ignorada, pois é a impermeabilização das paredes de concreto que torna toda a estrutura especialmente resistente e garante uma longa vida útil. Os materiais impermeabilizantes, além da proteção direta contra a absorção de umidade, conferem à superfície do concreto resistência à Baixas temperaturas, e aumentar a dureza do material.
Pela sua estrutura, os blocos de concreto são muito higroscópicos, portanto, se essas paredes de concreto não forem totalmente impermeabilizadas, o edifício começará a desabar em um período muito curto de tempo.
Todo o processo de impermeabilização pode ser dividido em três etapas:
- impermeabilização realizada durante o processo de mistura da mistura de concreto para blocos;
- impermeabilizar a superfície acabada;
- impermeabilização operacional.
Ainda no processo de preparação da mistura para blocos de concreto, vale a pena pensar em reduzir a higroscopicidade do material de construção resultante, por isso é adicionada à mistura de concreto uma substância especial que aumenta a resistência à água do material e protege o concreto ao longo toda a sua espessura. Tais materiais incluem o admix Penetron.
Depois de pronta a superfície de concreto, também é necessário realizar a impermeabilização superficial, bem como a impermeabilização das juntas, para isso utilizam-se as seguintes misturas: penebar, penecrete e penetron.
Além disso, durante a operação da edificação, deve-se monitorar cuidadosamente a integridade da superfície de concreto e, se necessário, cobrir eventuais fissuras ou fissuras com compostos especiais.
A impermeabilização é uma etapa fundamental na construção de estruturas de concreto, que garante resistência e longa vida útil.
Como desmontar paredes de concreto com rapidez e eficiência?
Ao conduzir trabalho de reparação ou reforma, bem como caso haja necessidade de demolição do prédio, as paredes de concreto são desmontadas. Como o concreto é altamente durável, o processo de desmontagem dessas paredes de concreto pode apresentar certas dificuldades.
As principais ferramentas utilizadas para a desmontagem são diversas ferramentas de impacto: marretas, cinzéis, martelos perfuradores, além de novos dispositivos modernos, como cunhas hidráulicas e corte diamantado.
O corte diamantado permite a desmontagem em pouco tempo e praticamente sem ruído, cortando blocos de concreto em pedaços do tamanho desejado.
Apesar da alta resistência das paredes de concreto, se necessário, é possível desmontar a estrutura em tempo curto, usando ferramentas modernas.
a. Preenchimento da fôrma com mistura de concreto
Para estruturas de concretagem em fôrmas deslizantes, são utilizadas misturas de concreto com grau de cimento Portland de pelo menos 400 com início de pega no máximo 3 horas e término da pega no máximo 6 horas. deverá ser determinada a concretagem e o levantamento da fôrma deslizante.
O abatimento cônico da mistura de concreto utilizada deverá ser: com compactação vibratória 6-8 e compactação manual 8-10 cm, e W/C - não superior a 0,5. O tamanho do grão do agregado graúdo não deve ser superior a /6 menor tamanho seção transversal da estrutura de concreto e para estruturas densamente armadas - não mais que 20 mm.
A espessura das paredes e vigas erguidas em fôrmas deslizantes, via de regra, não deve ser inferior a 150 mm (o peso do concreto deve ser maior que as forças de atrito), e o volume do concreto por 1 linear. m sua altura não deve exceder 60 l3.
Inicialmente, a fôrma é preenchida com uma mistura de concreto em duas ou três camadas até uma altura igual à metade da fôrma, por no máximo 3,6 horas. A segunda e terceira camadas são colocadas somente após a colocação da camada anterior em todo o perímetro. da cofragem. O posterior enchimento da cofragem só é retomado após o início do seu levantamento e termina o mais tardar após 6 horas.
Antes de encher a fôrma com mistura de concreto em toda a sua altura, ela é elevada a uma velocidade de 60-70 mm/h.
b. Processo de compactação de mistura
Após o enchimento inicial da fôrma em toda a altura, após novo levantamento, a mistura de concreto é colocada continuamente em camadas de até 200 mm de espessura em paredes finas (até 200 mm) e não mais que 250 mm nas demais estruturas. Uma nova camada é colocada somente após a camada anterior ter sido colocada, antes de começar a endurecer.
Durante o processo de betonagem, o nível superior da mistura aplicada deve estar mais de 50 mm abaixo do topo dos painéis de fôrma.
A mistura de concreto é compactada por meio de vibradores de haste com eixo flexível ou manualmente por meio de parafusos. O diâmetro da ponta vibratória deve ser de 35 mm para espessuras de parede até 200 mm e 50 mm para espessuras maiores.
Durante o processo de compactação da mistura, recomenda-se levantar e abaixar o vibrador em 50-100 mm dentro da camada a ser colocada, enquanto a ponta do vibrador não deve encostar na fôrma ou armadura, e não deve atingir o previamente colocado camada de fixação de concreto.
O ritmo de assentamento da mistura de concreto e levantamento da fôrma deve excluir a possibilidade de aderência do concreto assentado à fôrma e garantir a resistência do concreto que sai da fôrma, suficiente para manter a forma da estrutura e ao mesmo tempo permitindo para facilitar a remoção de vestígios de cofragem na sua superfície.
c. Rupturas durante a concretagem
Os intervalos entre o levantamento da fôrma não devem ultrapassar 8 minutos no caso de vibradores e 10 minutos na compactação manual da mistura de concreto. A taxa de elevação da cofragem a uma temperatura exterior de +15, +20° C e utilizando cimento Portland M 500 atinge 150-200 mm por hora.
Durante o processo de concretagem de paredes em fôrmas deslizantes, podem ocorrer “quebras” do concreto: a fôrma carrega consigo parte do concreto fraco da parede, com isso se formam cavidades e a armadura fica exposta. Os principais motivos de “falhas” são os seguintes: contaminação da fôrma; não conformidade com a conicidade da fôrma; longas pausas durante a concretagem.
Nos casos de ruptura forçada da betonagem, devem ser tomadas medidas para evitar a aderência do betão colocado à fôrma; a fôrma é elevada lentamente até que uma lacuna visível seja formada entre a fôrma e o concreto, ou periodicamente elevada e abaixada dentro de um degrau de macaco (“degrau no lugar”). Ao retomar a concretagem é necessário limpar a fôrma, retirar a película de cimento da superfície do concreto e lavar com água.
Durante o processo de betonagem, os vestígios de movimento da cofragem e pequenas cavidades na superfície exterior dos edifícios a betonar e no interior dos silos, bunkers e salas são imediatamente esfregados com uma argamassa de cimento de composição 1:2 após o betão sair da cofragem.
d. Fornecimento de mistura
Uma esteira ou lona é fixada nas bordas inferiores da fôrma para proteger o concreto fresco do ressecamento (hipotermia) e no verão é regada regularmente por meio de um duto circular.
Os blocos de janelas e portas em edifícios e estruturas são instalados durante a movimentação da fôrma, para a qual são pré-preparados (anti-séptico, recobertos com papel de cobertura) de acordo com as exigências do projeto. Para reduzir para 10 mm os vãos entre as paredes da fôrma e a caixa de bloco, são costuradas ripas na caixa, que são posteriormente retiradas. O reforço ao redor do bloco é instalado de acordo com o projeto.
O concreto é colocado próximo aos blocos instalados em ambos os lados simultaneamente. Após a cofragem subir acima dos blocos instalados, as ripas provisórias são removidas.
Para fornecer mistura de concreto, armaduras, macacos e outras cargas à fôrma, são utilizados guindastes de torre, guinchos de minas e guindastes autoelevatórios.
Bombas de concreto e sopradores pneumáticos também são utilizados para fornecer a mistura. Após a conclusão da construção da estrutura, a fôrma deslizante e todas as estruturas e equipamentos nela montados são desmontadas de forma que, após a retirada das peças individuais, seja garantida a estabilidade e segurança dos demais elementos.
Os canais em concreto formados pela movimentação dos tubos de proteção devem ser cuidadosamente vedados após a retirada dos macacos.
e. Pisos pré-fabricados
Ao construir estruturas em condições de inverno, o concreto é aquecido em estufas especialmente construídas acima do piso de trabalho e em andaimes externos usando vapor ou aquecedores elétricos ou radiação infravermelha.
Lajes de vários andares, lances de escadas e patamares são concretados com fôrmas de estoque adicionais ou montados a partir de elementos pré-fabricados. Neste último caso, durante a construção de um edifício ou estrutura, a necessidade de alterações e dispositivos adicionais em cofragem deslizante.
Pisos pré-fabricados podem ser instalados com guindaste de torre após a montagem das paredes em “poço” em toda a altura do edifício. Neste caso, as lajes repousam sobre inventário especial, suportes removíveis, fixados nas paredes logo abaixo de uma série de pequenas aberturas na parede. Barras de reforço são passadas pelas aberturas e conectadas às saídas das lajes. A união das paredes externas às lajes é realizada por meio de ranhuras nas paredes. Essa tecnologia garante a continuidade da concretagem, construção de paredes rápida e de alta qualidade.
Pisos monolíticos podem ser concretados após a construção das paredes do edifício em “poço”. Painéis de cofragem de inventário e dispositivos de suporte (cremalheiras telescópicas metálicas e travessas deslizantes) são transferidos de piso a piso por guindaste de torre ou manualmente.
Pisos monolíticos também podem ser concretados por meio de fôrmas suspensas rebaixadas montadas em uma plataforma especial. Este método é especialmente eficaz se bombas de concreto ou sopradores pneumáticos forem usados para fornecer a mistura de concreto.
f. Concretagem de pisos
Concretagem de pisos com defasagem de 1 a 2 andares atrás das paredes de concretagem, o processo de construção do edifício é complicado pela necessidade de paradas frequentes no levantamento de fôrmas deslizantes.
O método de concretagem cíclica combinada de paredes e pisos consiste no fato de que a concretagem das paredes em fôrmas deslizantes para cada vez na marca do piso seguinte. A fôrma vazia das paredes é colocada acima desta marca de forma que entre o fundo da fôrma deslizante e a marca do fundo do piso fique um vão igual à espessura do futuro piso. Ao mesmo tempo, os painéis de fôrma das paredes externas, bem como as fôrmas que formam a superfície interna dos poços dos elevadores e outras células que não possuem teto, são maiores em altura que os painéis do restante da fôrma. A betonagem dos pisos é efectuada através de painel ou fôrma seccional, sendo os painéis do piso de trabalho retirados após parada e alinhamento da fôrma deslizante.
A construção de edifícios e estruturas com 40-50 m de altura em betão armado monolítico pelo método de cofragem deslizante, de acordo com os principais indicadores técnicos e económicos, situa-se ao nível da construção a partir de estruturas pré-fabricadas de betão armado, e da construção de arranha-céus civis edifícios apresenta uma série de vantagens: redução do tempo de construção; redução da intensidade de mão-de-obra e do custo estimado da construção, inclusive através da redução de investimentos de capital específicos na base da indústria da construção; aumentando a confiabilidade, durabilidade e rigidez das estruturas devido à solidez e ausência de juntas, o que é especialmente valioso durante a construção em áreas sísmicas, em minas e solos de subsidência.
g. Construção de edifícios altos
Atrás últimos anos desenvolvido e implementado em nosso país nova maneira construção de edifícios altos de concreto armado monolítico na cofragem deslizante de um sistema sem haste, constituído por dispositivos hidráulicos ou pneumáticos de elevação de suporte que proporcionam um suporte confiável, comprimindo a parte construída das paredes com garras especiais e criando forças de atrito de suporte.
Com base nas propostas do Donetsk PromstroyNIIproekt, foi criado um modelo piloto de produção de fôrmas móveis, composto por duas seções de apoio-elevação (inferior e superior) apoiadas nas paredes da estrutura em construção, elevadores eletromecânicos de parafuso sem-fim, fôrmas deslizantes formas e molduras para fixação. Utilizando esta fôrma, durante a construção da planta de minério de ferro de Zaporozhye, foram erguidos os suportes das torres das galerias de transporte do armazém de minério do alto-forno.
Os suportes da torre que estão sendo erguidos têm diâmetro externo 6 me altura 14 m, espessura da parede é 300 mm. A construção de uma torre foi realizada por uma equipe de cinco pessoas. A velocidade média de concretagem atingiu 0,3 m/h sendo a velocidade da máquina de levantamento da fôrma durante o processo de assentamento e compactação da mistura de concreto de 0,6. m/h. Neste caso, a seção inferior do dispositivo de elevação repousava sobre concreto com resistência de 10 a 12 horas. O degrau dos trechos de elevação de 2 m permitiu a concretagem contínua por 6 a 6,5 horas.
h. Cofragem trepante
A cofragem trepante é utilizada na construção de estruturas de secção variável em altura, incluindo chaminés, torres de resfriamento hiperbólicas, torres de televisão e outros objetos altos. O elemento principal desta fôrma é um elevador de mina com plataforma de trabalho, ao qual é fixado um conjunto de fôrmas externas e internas ajustáveis.
O design do elevador permite que ele seja aumentado periodicamente por cima ou por baixo. Após cada ciclo de instalação dos painéis de fôrma, reforço e assentamento da mistura de concreto, a plataforma de trabalho é novamente elevada e a fôrma é reorganizada.
A cofragem para chaminés até 320 m de altura é composta por elementos externos e painéis interiores, anéis de rolamento, estrutura (suporte), mecanismos de movimento radial, plataforma de trabalho, andaimes suspensos, bem como talha de mina pós-montada com cabeçote de elevação, montada a partir de seções tubulares de 2,5 metros e equipada com gaiola de carga e carga -elevador de passageiros.
A cabeça de elevação, instalada num elevador com capacidade de elevação de 25 e 50 toneladas, sobe a uma velocidade de até 3 mm/s ao mover a cofragem para o nível seguinte. O degrau de trabalho para elevação da fôrma é de 2,5 m.
eu. Concretagem de eixo de tubo
A cofragem é constituída por duas cascas - exterior e interior, que são montadas a partir de painéis em chapa de aço com 2 mm de espessura, aparafusados.
A cofragem exterior das chaminés é constituída por painéis rectangulares e trapezoidais com 2,5 m de altura. A combinação destes painéis permitirá obter uma superfície cónica do tubo.
A fôrma externa é suspensa no anel de suporte que, quando o perímetro do tubo é reduzido, é substituído por um novo de menor diâmetro.
Para facilitar o assentamento do concreto, a fôrma interna é montada a partir de painéis de 1250x550 mm.
Concretagem de poço de tubulação: diagrama de organização do trabalho; desenvolvimento da fôrma trepante externa da chaminé cônica; painéis retangulares; painéis trapezoidais; c - painel da casca interna da fôrma; dossel coberto; cobertura protetora; elevador de minas; plataforma de forro; grampo; site de Trabalho; funil de distribuição; balde de carga; cabeça de levantamento; elevador de carga-passageiros; telfer; gaiola de carga; Cabeça de gato; sobreposição de tiras; tiras de aço; tiras de aço; chapa de aço com 2 mm de espessura.
Para dar rigidez aos painéis, são soldadas sobreposições nas bordas superior e inferior, com o auxílio das quais os painéis são montados em altura. COM fora Nas blindagens são soldados ilhós, nos quais são colocadas barras de reforço de 10-14 mm, formando uma série de anéis horizontais elásticos.
j. Construção de carcaças de torres de resfriamento
As blindagens são instaladas em duas (às vezes três) camadas. A fôrma da segunda camada é instalada após a colocação do concreto na fôrma da primeira camada. 8-12 horas após a colocação do concreto na segunda camada, a fôrma externa é removida e instalada na próxima posição mais alta. Após a instalação da armadura da terceira camada, a camada inferior da fôrma interna é removida e reorganizada para cima. Então o ciclo se repete. O reforço é instalado manualmente por meio de hastes individuais.
A mistura de concreto é alimentada pela caçamba da gaiola de carga para a tremonha receptora localizada no local de trabalho, depois para a tremonha móvel da pavimentadora de concreto e daí ao longo do tronco até a fôrma. A mistura de concreto é compactada por meio de vibradores profundos com eixo flexível.
A taxa de concretagem de troncos de chaminé a uma temperatura externa de 15-20° C atinge 1-1,5 m3/dia.
A construção das carcaças das torres de resfriamento é realizada por meio de uma unidade, que é uma torre treliçada (extensível), em cuja cabeça giratória são montadas lanças rotativas, às quais são fixados os painéis de fôrma trepantes, bem como os berços de trabalho.
A mistura de concreto é fornecida à plataforma superior do berço na caçamba vibratória por um telpher que se move ao longo da lança. A concretagem é realizada em camadas, semelhante à concretagem de chaminés.
2. Métodos de concretagem de estruturas
a. Concretagem em fôrma deslizante
Métodos especiais de concretagem de estruturas. A concretagem em fôrmas deslizantes é utilizada na construção de paredes de chaminés, torres de trabalho de elevadores e silos, cabeceiras, torres de água, bem como esquadrias de edifícios de vários andares. Os elementos estruturais dos edifícios e estruturas erguidos em fôrmas deslizantes devem ser verticais, o que é ditado pela característica principal da fôrma deslizante.
O método de concretagem de edifícios e estruturas monolíticas de concreto armado em fôrmas deslizantes é um processo de construção altamente organizado e amplamente mecanizado e com velocidade de fluxo. A instalação da fôrma, armadura, assentamento e compactação da mistura de concreto, decapagem do concreto são realizadas de forma combinada e contínua durante o processo de levantamento da fôrma (SNiP N1-B.1-70).
A cofragem deslizante inclui: painéis de cofragem, caixilhos de macaco, piso de trabalho com cobertura ao longo do contorno exterior da cofragem, andaimes suspensos, equipamentos para elevação de cofragens.
Os painéis de cofragem são fabricados com alturas de inventário de 1100-1200 mm a partir dos seguintes materiais: chapa de aço com espessura mínima de 1,5 mm; planejado tábuas de madeira espessura de pelo menos 22 mm; contraplacado impermeável com 8 mm de espessura; compensado cozido com 7 mm de espessura ou fibra de vidro com 3 mm de espessura. Em alguns casos, são feitos painéis de madeira-metal, nos quais a moldura é feita de perfis de aço laminado e o revestimento é feito de tábuas aplainadas ou compensados. Os círculos para fixação dos painéis de fôrma são geralmente feitos de perfis de aço laminado.
b. Construção de estruturas não padronizadas
Os painéis de fôrma metálicos são utilizados na construção de diversas estruturas semelhantes (silos, chaminés, tanques), quando as paredes laterais absorvem a alta pressão da mistura de concreto recém-assentada e, além disso, é garantida a rotação múltipla dos painéis de fôrma.
Painéis de madeira e madeira-metal apresentam menor rigidez e rotatividade, mas ao mesmo tempo menor custo em relação aos metálicos. São utilizados na construção de edifícios residenciais e civis onde a espessura das paredes não ultrapassa 200 mm, bem como em climas secos e quentes para proteger o concreto do superaquecimento.
Promissores são os painéis de cofragem feitos de compensado impermeável e fibra de vidro. Eles são duráveis e mais leves que os escudos feitos de outros materiais, mas ainda são mais caros.
Para a construção de estruturas não padronizadas, são utilizadas fôrmas de madeira não padronizadas. Por design, os painéis de inventário de cofragem deslizante são utilizados em dois tipos: bloco grande e bloco pequeno.
Em escudos de blocos grandes, os círculos de metal são rigidamente fixados ao revestimento. Esses escudos são fortes, duráveis e relativamente fáceis de montar.
Nos painéis de pequenos blocos, apenas os círculos metálicos que formam a moldura das paredes são rigidamente conectados entre si, e os painéis de cofragem são pendurados nos círculos sem fixá-los entre si.
3. Concretagem de bases e pisos
a. Preparação de concreto
Pisos e fundações de concreto (preparações) tornaram-se difundidos em edifícios industriais e civis.
A preparação do concreto é realizada principalmente em oficinas industriais térreas para pisos de cimento e asfalto, pisos de lajes de ferro fundido, blocos de madeira de ponta e outros tipos de pisos com espessura de 100-300 mm em solo preparado e nivelado. Para fundações de concreto, geralmente são utilizadas misturas de concreto rígido dos graus 100, 200 e 300.
Os pisos de concreto e cimento-areia são feitos de concreto ou argamassa com até 40 mm de espessura, conforme preparação. Em edifícios de vários andares, a fundação geralmente é composta por pisos de concreto armado.
Os trabalhos de instalação de pisos de concreto monocamada em edifícios térreos incluem: preparação de fundações de solo; instalação de placas de farol; receber e nivelar a mistura de concreto; rejuntamento de superfícies ou engomadoria.
Antes do início da preparação do concreto, devem ser concluídos todos os trabalhos subterrâneos de construção de fundações, canais, túneis, etc., concluído o aterro das fossas de escavação, nivelamento e compactação do solo.
Preparando a base do solo. Para solos densos, a mistura de concreto é colocada diretamente sobre o solo graduado. Solos a granel e estruturalmente perturbados nas fundações devem ser compactados mecanicamente. Em locais inacessíveis aos mecanismos de compactação, a espessura da camada de solo compactada com socadores manuais não deve ultrapassar 0,1 m.
b. Técnicas para concretagem de pisos
Solos sujeitos a recalques significativos são substituídos ou reforçados. Neste último caso, a preparação do concreto é reforçada com malha.
Antes de colocar o preparo de concreto sobre ele, uma camada de brita ou cascalho com espessura de 60-150 mm é compactada ou rolada com rolos na superfície da base de solos moles. Antes de instalar pisos em solos argilosos saturados de água, argilosos e empoeirados, é necessário baixar o nível lençóis freáticos e seque a base até que a capacidade de suporte projetada seja restaurada. Em solos elevados, o piso deve ser instalado de acordo com as instruções de projeto.
É proibido nivelar e compactar solo com mistura de solo congelado, bem como neve e gelo. A instalação de pisos de concreto em solos congelados também não é permitida.
Técnicas de concretagem de pisos e fundações. Antes da concretagem, as placas balizas são instaladas niveladas de forma que sua borda superior fique no nível da superfície do preparo de concreto (Fig. 14, a). A distância entre as placas depende do comprimento da mesa vibratória e geralmente é de 3 a 4 m. As placas do farol são fixadas com estacas de madeira cravadas no solo. Pisos e bases são concretados em faixas alternadas, começando pelos locais mais distantes da passagem.
c. Preparações de concretagem
As faixas intermediárias são concretadas após o endurecimento do concreto das faixas adjacentes. Antes da concretagem das faixas intermediárias, são retiradas as placas do farol. O comprimento das tiras é considerado o maior possível. A camada de mistura de concreto em preparação antes de ser nivelada e compactada deve ultrapassar o nível das placas do farol em 2 a 3 cm.
A mistura de concreto é compactada com uma ripa vibratória, que é uma viga metálica (canal, viga I), na qual são montados um ou dois motores elétricos de um vibrador de superfície.
Na concretagem de preparações e revestimentos de pisos, cada área vibrada deve ser coberta com uma betonilha vibratória de 150 mm e metade de sua largura, respectivamente.
Técnicas de concretagem de pisos e bases: esquema de concretagem de base para pisos; ferramentas manuais para alisar superfícies de betão; base lançada; preparação para a fundação; apostas; cofragem lateral; raspador com elástico para retirar a leitada; passadeira; ralador; Tabua de passar; elástico de borracha.
Dependendo das condições da obra, o assentamento da mistura de concreto com pavimentadoras de concreto nas fundações é feito de duas formas: “pull-on”, quando a unidade se desloca atrás da frente de concretagem, e o concreto na área da unidade. a ação tem tempo para ganhar a resistência necessária ao seu movimento, e o “pull-on”, quando o mecanismo avança à frente da frente de concretagem, pois o concreto não tem tempo para ganhar a resistência necessária.
d. Produção de mistura de concreto
O primeiro método é preferível, pois cria uma ampla gama de trabalhos de preparação da base. Com o segundo método, os trabalhos preparatórios antecipam o assentamento da mistura de concreto em uma seção, cujo comprimento é igual ao raio de ação do mecanismo.
Em salas não aquecidas em preparação de concreto, juntas termorretráteis longitudinais são instaladas a cada duas faixas e juntas transversais termorretráteis a cada 9-12 m ao longo do comprimento das faixas, que dividem a área concretada em lajes separadas medindo 6X9-9X12 m.
As costuras longitudinais são feitas através da instalação de tábuas aplainadas revestidas com betume quente ou tábuas envoltas em feltro. Após a pega do concreto, as tábuas são removidas e as costuras preenchidas com betume. As costuras também são feitas revestindo as bordas laterais das tiras com uma camada de betume de 1,5-2,0 mm antes de colocar a mistura de concreto nos espaços adjacentes.
Para formar juntas de dilatação transversais (semi-juntas), são utilizadas tiras metálicas com largura de 60-180 e espessura de 5-7 mm, que durante o processo de concretagem são colocadas em preparação a 73 de sua largura e removidas após 30 -40 minutos. Após o endurecimento total do concreto, as depressões resultantes são limpas e preenchidas com betume grau III ou argamassa de cimento.
e. Superfície de bases de concreto
Em locais onde haja ruptura na concretagem de bases e pisos, não é permitida a instalação de betonilha vibratória na borda da camada assentada, pois isso fará com que a mistura de concreto escorregue e deslamine. Portanto, ao final do turno de trabalho, é instalada uma divisória feita de tábuas nos locais onde há ruptura planejada na concretagem, e a última porção da mistura de concreto é nivelada e vibrada ao longo dela.
A superfície das bases de concreto deve ser limpa de detritos e película de cimento antes de colocar revestimentos de piso contínuos usando ligante de cimento ou materiais de peça usando argamassa de cimento e areia.
Nas fases iniciais do concreto, escovas mecânicas de aço são utilizadas para esse fim. Se o concreto for muito resistente, ranhuras de 5 a 8 mm de profundidade são aplicadas em sua superfície a cada 30 a 50 mm usando ferramentas pneumáticas. Isto permite obter uma superfície rugosa para a camada subjacente e garantir uma melhor aderência à camada superior.
Os revestimentos para pisos de concreto ou cimento-areia consistem em uma camada de concreto ou argamassa de 20-40 mm e são concretados da mesma forma que a preparação em faixas de 2-3 m de largura, uma em outra.
Antes da concretagem do revestimento, ripas de madeira do farol ou esquadrias metálicas são fixadas na superfície da base de concreto. A mistura de concreto é compactada com ripas vibratórias e a superfície do concreto é nivelada com uma ripa de madeira movimentada ao longo da faixa.
f. Leite de cimento
A leita de cimento que vem à superfície durante a compactação de bases de concreto e revestimentos de piso é removida com um raspador com elástico.
Para pequenos volumes de trabalho, a superfície do piso de concreto é finalmente acabada com tábua de passar ou fita de lona emborrachada, cujo comprimento deve ser 1-1,5 m maior que a largura da faixa de concreto. As pontas da fita são fixadas em rolos que servem como alças; a largura da fita é de 300-400 mm. Alise a mistura de concreto compactado 25-30 minutos após o assentamento. Quando a fita é movida alternadamente através e ao longo da tira, a fina película saliente de água é removida da superfície do concreto e o piso de concreto é pré-alisado. O nivelamento final da superfície é realizado após 15-20 minutos com movimentos mais curtos da fita.
Dar Piso de concreto de alta resistência à abrasão, sua superfície é tratada com espátula metálica aproximadamente 30 minutos após o nivelamento final, expondo os grãos de brita. Se não for necessária alta resistência à abrasão, um piso de argamassa de cimento é instalado na preparação de concreto.
Se for necessário instalar um piso de duas camadas ao mesmo tempo, primeiro a camada inferior é colocada entre as placas de balizamento e compactada com um vibrador de área ou uma mesa vibratória instalada obliquamente, depois com um intervalo de não mais que 1,5-2 horas ( para melhor ligação da camada inferior com a superior), é feito um piso limpo.
e. Engomar superfície de concreto
Para grandes volumes de trabalho, a superfície de um piso de concreto limpo durante o período de endurecimento inicial é friccionada com uma máquina SO-64 (ou OM-700), composta por um disco de espátula com diâmetro de 600 mm, um motor elétrico e um alça de controle. Girando a 140 rpm, o disco da espátula nivela e alisa a superfície do piso de concreto. Produtividade da máquina 30 m2/h.
A passagem a ferro da superfície de concreto é usada para aumentar a densidade do piso. Consiste em esfregar cimento seco e peneirado na superfície do concreto úmido até que apareça um brilho uniforme. Superfícies de concreto secas são umedecidas com água antes de passar. A engomagem pode ser feita manualmente com espátula de aço ou com espátula SO-64.
Uma variedade de pisos de concreto são de mosaico, feitos de uma mistura que inclui: cimento Portland branco ou colorido, lascas de mármore, granito ou basalto e corante mineral. Uma camada de mosaico com 1,5-2 cm de espessura é geralmente colocada sobre uma camada subjacente de argamassa de cimento de aproximadamente a mesma espessura. A limitação dos campos monocromáticos e a execução dos padrões previstos no projeto são realizadas por meio de tiras de veios de vidro, cobre ou latão, embutidas na camada subjacente de argamassa. Essas tiras são posicionadas de forma que suas nervuras superiores sirvam de baliza no assentamento e nivelamento da camada de mosaico.
As superfícies dos pisos de mosaico são acabadas com máquinas elétricas após o endurecimento do concreto (após 2-3 ou mais dias). Após o primeiro lixamento, os defeitos encontrados na superfície do piso são betumados com argamassa colorida de cimento-areia. Em seguida, o piso é lixado com abrasivos mais finos, tratado com pós de polimento e lustrado em máquina de polir.
4. Pilares de concretagem
a. Fôrma para pilares retangulares
Os pilares como elemento da moldura de edifícios e estruturas são de seção retangular, poligonal e circular. A altura das colunas atinge 6 a 8 m ou mais.
A cofragem de pilares retangulares é uma caixa de dois pares de painéis (madeira, metal ou combinados). A pressão lateral da mistura de concreto é percebida por pinças que comprimem a caixa. Os grampos são feitos de grampos de metal quando a rotação da fôrma é alta e os grampos de madeira são usados quando a rotação da fôrma é baixa. Os furos nas tiras da braçadeira metálica para fixação das cunhas permitem sua utilização em colunas de diversas seções. Para limpar a caixa, é feito um furo provisório na parte inferior de um dos painéis. As formas de bloco também são utilizadas para pilares de concretagem.
Painéis padronizados típicos e painéis de cofragem são fixados a blocos de reforço com tirantes e amarrados com tirantes. A fôrma dos pilares baixos é fixada em duas direções perpendiculares entre si por meio de juntas inclinadas (contraventamentos). Quando a altura dos pilares é superior a 6 m, as caixas de cofragem são fixadas em andaimes especialmente dispostos.
Após a instalação da fôrma dos pilares, são feitos furos de 500x500 mm e plataformas de trabalho para concretagem a cada 2-3 m de altura. A fôrma de pilares altos pode ser instalada apenas em três lados, sendo que no quarto lado pode ser ampliada durante a concretagem.
b. Colunas de concretagem
Para colunas redondas, são feitos moldes especiais de blocos de metal.
O cumprimento da espessura da camada protetora dos pilares é garantido por espaçadores de cimento especiais, que, antes da concretagem, são fixados às barras de armadura por meio de um fio de ligação embutido nos espaçadores durante sua fabricação.
A concretagem de pilares com dimensões transversais de 400 a 800 mm na ausência de pinças de interseção é realizada por cima sem interrupção em trechos de até 5 m de altura. Pilares com seção lateral inferior a 400 mm e pilares de qualquer seção com pinças de interseção. , que contribuem para a delaminação da mistura de concreto durante sua queda, são concretadas lateralmente em áreas com altura não superior a 2 m.
Cofragem de pilares: caixa montada; braçadeira de metal de estoque; pinça de madeira com cunhas; detalhe de montagem de pinça de madeira; caixa; braçadeira de inventário de metal; cunhas que prendem os grampos; moldura para cofragem de pilares; limpeza da porta do furo; painéis de cobertura; furos para cunhas, painéis embutidos; impulso morre.
Se os trechos dos pilares concretados sem juntas de trabalho estiverem em alturas maiores, é necessário fazer quebras para permitir a sedimentação da mistura de concreto. A duração do intervalo deve ser de no mínimo 40 minutos e no máximo 2 horas.
c. Estruturas de quadros
Nos casos em que os pilares fazem parte de uma estrutura de pórtico e acima deles existem vigas ou terças com armadura densa, é permitida a concretagem primeiro dos pilares e, a seguir, após a instalação da armadura, as vigas e terças.
Na concretagem por cima, recomenda-se preencher inicialmente a parte inferior da fôrma dos pilares até uma altura de 100-200 mm com argamassa de cimento de composição 1:2-1=3 para evitar o acúmulo de agregado graúdo sem argamassa na base da coluna. Quando uma porção da mistura de concreto cai de cima, grandes partículas de agregado ficam embutidas nesta solução, formando uma mistura de composição normal.
A mistura de concreto nos pilares é compactada por meio de vibradores internos com eixo flexível ou rígido. A compactação com vibradores externos fixados na fôrma de pilares de pequena seção é menos eficaz e praticamente não é utilizada.
Para evitar a formação de cavidades durante a concretagem dos pilares (principalmente dos cantos), é muito útil bater com um martelo de madeira pelo lado de fora, ao nível ou ligeiramente abaixo da camada de mistura de concreto a ser colocada.
A concretagem dos pilares de acordo com SNiP III-B.1-70 é realizada em toda a altura sem costuras de trabalho. É permitida a instalação de juntas de trabalho: ao nível do topo da fundação, na parte inferior das terças e vigas ou consoles de guindaste e no topo das vigas de guindaste.
d. Concretagem de estruturas de pórticos
Em colunas de pisos sem vigas, é permitida a instalação de costuras na parte inferior das colunas ou na parte inferior dos capitéis. Os capitéis são concretados simultaneamente à laje.
A superfície das juntas de trabalho realizadas no assentamento intermitente da mistura de concreto deve ser perpendicular ao eixo dos pilares a serem concretados.
A concretagem das estruturas do pórtico deve ser realizada com intervalo entre o assentamento da mistura de concreto nos pilares (cremalheiras) e nas travessas do pórtico. As costuras de trabalho são colocadas alguns centímetros abaixo ou acima da junção da barra transversal do quadro com o rack.
As paredes (incluindo divisórias) podem ser de seção transversal constante e variável, verticais e inclinadas, redondas, curvas, poligonais e de planta reta.
Na concretagem de paredes e divisórias, são utilizados os seguintes tipos de fôrmas: painéis unificados padrão e painéis de fôrmas desmontáveis e ajustáveis, formas de bloco, fôrmas rolantes trepantes e ajustáveis, deslizantes e ajustáveis e deslizantes.
A fôrma desmontável de pequenos painéis é instalada em duas etapas: primeiro, de um lado, em toda a altura da parede ou divisória, e após a instalação da armadura, do outro. Se a espessura da parede for superior a 250 mm, formulários de inventário especiais serão instalados no segundo lado.
Ajustado para toda a altura da parede, em de outra forma- camada por camada durante o processo de concretagem. As fôrmas instaladas em toda a altura da parede possuem furos para o fornecimento da mistura de concreto através delas para a estrutura.
5. Paredes de concreto
a. Projetar espessura da parede
A cofragem para paredes até 6 m de altura é montada a partir de plataformas móveis ou andaimes leves. Em altitudes mais elevadas, são erguidos andaimes. A fôrma da parede é fixada com escoras ou escoras, tirantes ou amarradores de arame.
Para manter a espessura projetada das paredes, são instalados espaçadores de concreto ou madeira nos locais por onde passam as betonilhas. Estes últimos são removidos durante o processo de concretagem.
A fôrma desmontável de grandes blocos é instalada em camadas durante o processo de concretagem das paredes. Isso permite limitar-se a um conjunto de cofragens de apenas duas camadas. Todos os trabalhos do ciclo completo de concretagem de paredes nesta fôrma são realizados na seguinte sequência: primeiro é instalado ou construído o andaime (andaime), depois é processada a costura de trabalho da concretagem e instalada a armadura, após o que a fôrma é passou da camada inferior para a superior. O ciclo de concretagem de uma camada termina com o assentamento e compactação da mistura de concreto e posterior cura do concreto na fôrma.
Forma de bloco para cofragem: pinça de fixação nº 1; faixa de concreto armado; roupa de cama; macaco de parafuso; bloco de cofragem; elemento de vedação para 1ª camada de concretagem; painel de cofragem; braçadeira de fixação nº 2; piso de trabalho; elemento de vedação para 2º nível de concretagem; inserção de inventário; suporte deslizante; cunha dupla de madeira.
b. Bloquear formas de cofragem
As formas de cofragem em bloco são utilizadas na betonagem de paredes de altura e comprimento consideráveis, ou seja, quando é garantida a sua utilização repetida. A forma de bloco do projeto do Kharkovorgtehstroy Trust consiste em blocos, painéis, elementos adicionais e de fixação.
A rigidez dos blocos é garantida por contraventamentos horizontais e treliças de apoio, que também funcionam como andaimes. Para instalação, alinhamento e desmontagem de fôrmas, as treliças de suporte são equipadas com macacos. As dimensões dos blocos comuns são 3X8,3X2 e 1,5x3 m.
Fôrma rolante projetada por Donetsk PromstroyNIIproekt: carrinho; Coluna; feixe; guincho de levantamento de escudo; painel de cofragem; braçadeiras; escada; controles deslizantes; dispositivo de aperto; piso; cercas; bunker
O tabuleiro de blocos, painéis e extensões é montado a partir de painéis de pequeno porte confeccionados em cantos de 45X45x5 mm e chapa de aço com 3 mm de espessura. Nas nervuras da moldura da blindagem existem furos com diâmetro de 13 mm para fixação das blindagens entre si.
Se necessário, os blocos de cofragem montados podem ser desmontados em painéis separados. A fôrma de blocos é reorganizada camada por camada durante o processo de concretagem. Na concretagem de paredes de seção constante e variável, utilizam-se fôrmas rolantes (inclusive movidas horizontalmente sobre patins).
c. Construção de paredes
A concretagem das estruturas pode ser realizada em camadas com movimento contínuo ou cíclico da fôrma, bem como ao longo de alças ao longo de toda a altura da parede. A fôrma rolante projetada por Donetsk PromstroyNIIproekt consiste em dois painéis metálicos de 6 a 8 comprimentos e 1,3 m de altura. A estrutura dos painéis é feita de ângulo e o tabuleiro é feito de chapa de aço com 6 mm de espessura. Tamanho da cofragem 6700X X 5400X3900 mm, peso 800 kg. Usando dispositivos especiais - controles deslizantes - as blindagens são fixadas nas colunas guia do portal.
As colunas do portal na parte inferior repousam sobre um carrinho e na parte superior são conectadas por uma viga, o que permite espalhar as colunas na largura desejada (até 600 mm). A movimentação dos painéis perpendicularmente à superfície da estrutura de concreto é realizada por meio de dispositivo de parafuso, e o levantamento é feito por cabos através de blocos fixos montados em vigas de ligação. A fôrma é movimentada ao longo da parede de concreto por meio de guinchos de dupla face.
A construção de paredes em fôrmas deslizantes e trepantes é discutida a seguir, entre métodos especiais de construção de estruturas.
Na concretagem de paredes, a altura dos trechos erguidos sem interrupção não deve ultrapassar 3 m, e para paredes com espessura inferior a 15 cm - 2 m.
d. Fornecimento de mistura de concreto
Para maiores alturas de trechos de paredes concretadas sem juntas de trabalho, é necessário fazer pausas de no mínimo 40 minutos, mas não superiores a 2 horas, para assentar a mistura de concreto e evitar a formação de fissuras sedimentares.
Caso exista abertura de janela ou porta na parede a betonar, a betonagem deve ser interrompida ao nível do bordo superior da abertura ou deve ser colocada uma junta de trabalho (se possível) neste local. Caso contrário, formar-se-ão fissuras sedimentares perto dos cantos do molde. No fornecimento de mistura de concreto a partir de uma altura superior a 2 m, são utilizados troncos de ligação.
Na concretagem por cima, a parte inferior da fôrma da parede é primeiro preenchida com uma camada de argamassa de cimento de composição 112-1: 3 para evitar a formação de concreto poroso com acúmulo de agregado graúdo na base das paredes.
Na concretagem das paredes dos tanques para armazenamento de líquidos, a mistura de concreto deve ser aplicada continuamente em toda a altura em camadas não superiores a 0,8 vezes o comprimento da parte útil dos vibradores. Em casos excepcionais, as juntas de trabalho resultantes devem ser tratadas com muito cuidado antes da betonagem.
As paredes de grandes tanques podem ser concretadas em seções verticais, seguidas de processamento e preenchimento das juntas verticais de trabalho com mistura de concreto. As juntas entre as paredes e o fundo dos tanques são feitas de acordo com os desenhos de trabalho.
6. Betonagem de vigas, lajes, abóbadas
a. Concretagem de lajes nervuradas
Concretagem de vigas, lajes, abóbadas, arcos e túneis. Vigas, lajes e pisos são geralmente concretados em fôrmas desmontáveis a partir de painéis e painéis padronizados. Vigas e terças também são concretadas em blocos.
A cofragem para pavimentos nervurados é constituída por pequenos painéis de madeira apoiados em estantes deslizantes de madeira-metal a uma altura até 6 m e andaimes especialmente dispostos a uma altura superior a 6 m.
A fôrma da viga é composta por três painéis, um dos quais serve de fundo e os outros dois de vedação lateral das superfícies. Os painéis laterais da fôrma são fixados na parte inferior com placas de pressão costuradas na cabeceira da estante e na parte superior com fôrmas de laje.
Concretagem de lajes nervuradas: Forma geral andaimes e cofragens nervuradas para pavimentos; a localização das costuras de trabalho na concretagem de pisos nervurados no sentido paralelo às vigas secundárias; o mesmo para as vigas principais; cofragem de vigas; cofragem para lajes; circulado; cofragem de terça; cofragem de colunas; prateleiras deslizantes; painéis de pressão; suportes; frisos; painéis de cofragem para lajes; circulado; placas subcirculares; escudos laterais; inferior: cabeça do rack; posição de trabalho da costura (as setas indicam o sentido da concretagem).
b. Fôrma de piso sem vigas
Os painéis de cofragem para lajes são assentados lateralmente sobre círculos de tábuas, que por sua vez repousam sobre tábuas subcirculares pregadas nas tiras de costura dos painéis laterais da viga e apoiadas em cavaletes.
Para a fixação dos círculos e painéis laterais, são colocadas placas frisadas em todo o perímetro da laje, o que também facilita a retirada da fôrma da laje. Quando a altura das vigas é superior a 500 mm, os painéis laterais da fôrma são reforçados adicionalmente com fios de arame e espaçadores temporários.
A distância entre os postes e os círculos é determinada por cálculo. Os postes de suporte são fixados em direções perpendiculares entre si com cordas ou suportes de inventário.
A cofragem de um piso sem vigas é constituída pela cofragem de pilares, capitéis e laje. A fôrma para lajes é composta por dois tipos de painéis, dispostos em círculos entre frisos costurados no topo das estantes. Para apoiar os círculos, terças emparelhadas são feitas de tábuas apoiadas em racks. Os escudos dos capitéis repousam sobre a fôrma das colunas de um lado e são sustentados por círculos ao longo do contorno externo.
Na instalação de fôrmas suspensas para lajes em concreto armado pré-fabricado ou vigas metálicas, são instaladas alças de suspensão metálicas, dispostas ao longo das vigas em um determinado passo. Nestes laços são instaladas placas sobrecirculares, sobre as quais repousam os círculos e painéis da fôrma da laje.
c. Camada protetora
A concretagem dos pisos (vigas, terças e lajes) geralmente é realizada simultaneamente. Vigas, arcos e estruturas semelhantes com altura superior a 800 mm são concretadas separadamente das lajes, fazendo juntas de trabalho 2 a 3 cm abaixo do nível da superfície inferior, e se houver esquadros na laje - ao nível do parte inferior do esquadro da laje (SNiP Sh-V.1-70 ).
Para evitar fissuras sedimentares, a concretagem de vigas e lajes monoliticamente ligadas a pilares e paredes deve ser feita 1 a 2 horas após a concretagem desses pilares e paredes.
A mistura de concreto é colocada em vigas e terças em camadas horizontais, seguida de compactação com vibradores de eixo flexível ou rígido - em vigas potentes ou levemente reforçadas. A mistura de concreto é colocada nas lajes ao longo das ripas de balizamento, que são instaladas na fôrma por meio de calços em fileiras a cada 1,5-2 m. Após a concretagem, as ripas são retiradas e as depressões resultantes são alisadas. Nas lajes com armadura dupla, o nivelamento e a compactação da mistura de concreto são feitos a partir do piso ajustável para não dobrar a armadura superior.
As lajes são concretadas no sentido das vigas secundárias. A camada protetora em lajes, vigas e terças é formada por meio de espaçadores ou pinças especiais para argamassa de cimento. À medida que as estruturas vão sendo concretadas, a armadura é levemente sacudida por meio de ganchos metálicos, garantindo a formação de uma camada protetora com a espessura necessária sob a armadura.
d. Concretagem de pisos
A mistura de concreto em lajes de até 250 mm de espessura com armadura simples e até 120 mm de espessura com armadura dupla é compactada com vibradores de superfície, em lajes de maior espessura - com vibradores profundos.
Na concretagem de juntas planas, as juntas de trabalho podem ser colocadas em qualquer lugar paralelo ao lado menor da laje. Nos pisos nervurados, na concretagem paralela ao sentido das vigas principais, a costura de trabalho deverá ser disposta nos dois quartos intermediários do vão das terças e lajes, e na concretagem paralela às vigas secundárias, bem como nas vigas individuais, no terço médio do vão das vigas.
A superfície das juntas de construção em vigas e lajes deve ser perpendicular ao sentido da concretagem. Portanto, nos locais planejados onde é interrompida a concretagem das lajes, são instaladas tábuas na borda, e nas vigas - tábuas com furos para reforço.
As juntas de dilatação dos pisos são dispostas em consolas de pilares ou através da instalação de pilares emparelhados, garantindo a livre movimentação das vigas na costura no plano horizontal ao longo da chapa metálica de suporte.
Na concretagem de pisos em edifícios de vários andares, as plataformas receptoras são dispostas ao nível de cada andar, e no interior do edifício são instalados transportadores e calhas vibratórias para fornecer a mistura de concreto após içamento por guindaste até o local de instalação.
e. Abóbadas e arcos
Durante o processo de concretagem de revestimentos, pisos e vigas individuais, não é permitido carregá-los com cargas concentradas superiores às permitidas especificadas no projeto de obra.
Abóbadas e arcos de curto comprimento são concretados em fôrmas desmontáveis de pequenas peças ou grandes painéis apoiadas em estantes. Para a concretagem de abóbadas e arcos longos, utiliza-se uma fôrma rolante de estoque montada em um carrinho. Na parte inferior da fôrma são instalados círculos de elevação e abaixamento, sustentando um revestimento de duas camadas composto por tábuas assentadas com folga de 10 mm e compensado impermeável. A distância entre as tábuas reduz o risco de a fôrma ficar presa no arco durante o seu inchaço. O levantamento e o abaixamento dos círculos são feitos por meio de talhas e blocos, e toda a fôrma é movimentada ao longo dos trilhos por meio de um guincho.
As abóbadas e arcos de pequeno vão devem ser concretados sem: rupturas simultâneas de ambos os lados desde os apoios (talões) até ao meio da abóbada (castelo), o que garante a preservação da forma desenhada da fôrma. Se houver perigo de abaulamento da fôrma na fechadura da abóbada durante a concretagem das partes laterais, ela é carregada temporariamente.
Cofragem rolante da abóbada: secção transversal; corte longitudinal; apertando o arco-diafragma; prateleiras retráteis; talhas manuais.
7. O processo de concretagem de estruturas complexas
a. Arcos e abóbadas enormes
As abóbadas longas são divididas ao longo do seu comprimento em áreas limitadas de concretagem com juntas de trabalho localizadas perpendicularmente à geratriz da abóbada. O concreto é colocado em áreas limitadas da mesma forma que nas abóbadas curtas, ou seja, simetricamente dos calcanhares ao castelo.
Arcos maciços e abóbadas com vão superior a 15 m são concretados em faixas paralelas ao eixo longitudinal da abóbada. O assentamento da mistura de concreto em tiras também é feito simetricamente em ambos os lados, desde os calcanhares até a fechadura da abóbada.
Os vãos entre as faixas e seções das abóbadas longas são deixados com aproximadamente 300-500 mm de largura e são concretados com uma mistura de concreto rígido 5-7 dias após a conclusão da concretagem das faixas e seções, ou seja, quando ocorre o assentamento principal do concreto. .
Nas abóbadas íngremes, as áreas próximas aos apoios são concretadas em fôrma dupla-face, e a segunda fôrma (superior) é instalada com painéis separados durante a concretagem.
A mistura de concreto é compactada em arcos maciços e abóbadas com vibradores internos de eixo flexível ou rígido, dependendo do grau de armadura, em abóbadas de paredes finas - com vibradores de superfície. O aperto de abóbadas e arcos que possuam dispositivos de tensão deverão ser concretados após o aperto desses dispositivos e afrouxamento dos revestimentos. Amarrações rígidas sem dispositivos de tração poderão ser concretadas simultaneamente à concretagem do revestimento.
b. Túneis e tubulações
Túneis e tubulações são concretados em valas abertas e subterrâneas em fôrmas móveis desmontáveis e rolantes. A cofragem móvel de madeira para túnel de passagem curvilínea com secção transversal até 3 m é constituída por painéis em forma de círculos curvos, revestidos com tábuas aplainadas, contraplacado impermeável ou chapa de aço sobre calçadão. Os suportes que sustentam o piso de trabalho são costurados nos círculos dos painéis externos. A fôrma interna é composta por dois painéis, cujo fundo repousa sobre cunhas emparelhadas e o topo é conectado por meio de parafusos na fechadura da abóbada.
As fôrmas externa e interna são conectadas entre si por meio de tirantes. O comprimento dos painéis é normalmente de 3 m, a massa da fôrma chega a 1,5 toneladas. A fôrma externa e interna é movimentada por meio de um guincho ao longo de guias de madeira. A fôrma externa também pode ser movida para um novo local por meio de um guindaste. Fôrma rolante de madeira projetada por engenheiro. V.B. Carvalho para concretagem de túneis e esgotos retangulares é composto por trechos de 3,2 m de comprimento.
A secção interna da cofragem é constituída por quatro caixilhos de aço em forma de U revestidos com placas aplainadas, contraplacado ou chapa de aço. Cada moldura é composta por dois postes laterais e duas meias travessas, interligadas por três dobradiças. As molduras externas das seções de fôrma possuem no meio um suporte deslizante feito de tubos, apertados com macacos roscados. As estruturas são sustentadas por postes intermediários e vigas horizontais retráteis em um carrinho que se move ao longo de um trilho.
c. Abóbadas de estruturas de túneis
A secção externa da cofragem é composta por cinco pórticos com escoras e travessas destacáveis. Racks de quadro com dentro coberto com tábuas. A fôrma externa é fixada à fôrma interna com parafusos passados por terças removíveis. A fôrma permite a concretagem de túneis com largura de 2100-2800 mm e altura de 1800-2200 mm: o peso de uma seção da fôrma chega a 3 toneladas.
A cofragem externa geralmente é reorganizada por um guindaste. Ao desmontar a fôrma, os tirantes são removidos, as juntas das travessas são separadas: as molduras externas da fôrma, após o que a fôrma é removida. Para a retirada da fôrma interna, por meio de macacos disponíveis nas estantes externas, são baixadas meias-travessas com painéis de teto.
A concretagem dos túneis é realizada, via de regra, em duas etapas: primeiro o fundo e depois as paredes e tetos (abóbada) do túnel.
Os arcos das estruturas do túnel são concretados simultaneamente em ambos os lados, desde os calcanhares até o castelo, em camadas radiais. O castelo é concretado em camadas inclinadas ao longo da cobertura do arco, enquanto a fôrma é colocada à medida que a concretagem avança em seções curtas - de círculo em círculo.
Em abóbadas poderosas de estruturas de túneis, as juntas de construção devem ser radiais. A direção necessária das superfícies de costura é garantida pela instalação de painéis de cofragem. Antes da concretagem do castelo, deve-se retirar a película de cimento da superfície do concreto.
d. Acabamentos do túnel
É aconselhável betonar os acabamentos do túnel paralelamente à escavação, pois neste caso o período total de construção do túnel é reduzido. Porém, quando a seção transversal do túnel é pequena devido às condições restritas, o acabamento é erguido após a conclusão da escavação de todo o túnel ou de seções individuais entre as faces intermediárias.
O revestimento do túnel é concretado continuamente ao longo de toda a seção transversal da escavação, ou em partes na seguinte seqüência: bandeja do túnel, abóbada e paredes, ou vice-versa.
Atrás da fôrma, a mistura de concreto é fornecida pela extremidade ou através de escotilhas na fôrma por meio de bombas de concreto ou sopradores pneumáticos. A mistura de concreto também pode ser fornecida às paredes laterais e à calha do túnel por meio de carrinhos basculantes por meio de calhas de distribuição.
A mistura de concreto é compactada camada por camada por meio de vibradores profundos através de janelas na fôrma ou vibradores externos fixados na fôrma.
Se as paredes de acabamento do túnel forem concretadas após a abóbada (método “abóbada apoiada”), antes da betonagem, a fôrma é removida da superfície inferior dos pés da abóbada e a superfície é cuidadosamente limpa. As paredes são concretadas em camadas horizontais com a expansão simultânea da fôrma até um nível inferior à marca do fundo do arco em até 400 mm. O espaço entre a quinta abóbada e a parede adjacente é preenchido com uma mistura rígida de concreto e cuidadosamente compactado. Primeiramente, são colocados tubos na área de junção para posterior injeção de argamassa de cimento.
O concreto armado pré-fabricado, bem como as tecnologias de moldagem monolítica de paredes com fôrmas permanentes, permitem a construção de edifícios com qualquer número de andares. Neste caso, não só a resistência das estruturas de suporte, mas também a rapidez da sua construção é de grande importância. Afinal, em última análise, o preço do metro quadrado de área depende do tempo gasto na construção - e isso é objetivo principal desenvolvedor.
O concreto, como material de parede, também é popular hoje em dia na construção privada. Nesse sentido, surge a pergunta: “Como rebocar uma parede de concreto?” - é regularmente solicitado não apenas por moradores de arranha-céus pré-fabricados, mas também por proprietários de terrenos que planejam decorar as paredes de uma casa recém-construída com as próprias mãos.
Por muitas décadas, o gesso foi a principal forma de proteger o concreto da umidade e da corrosão, mas com o advento das impregnações hidrofóbicas de penetração profunda, esse problema se resolveu. É claro que, quando se trata de fachadas, o reboco de superfícies de concreto permanece sempre relevante.
- Mas no interior dos edifícios passou a ser realizado apenas para efeito de decoração ou nivelamento (ver) - quando há necessidade de fechar as juntas entre os painéis, e as paredes estão previstas para serem revestidas com azulejos, preparadas para pintura ou papel de parede. Acabamentos nomeados paredes interiores podem ser chamados de tradicionais, mas não são de forma alguma a única prerrogativa nesta matéria.
- A textura do concreto em si é muito atraente e os designers modernos, como sempre, a adotaram. Por exemplo, o reboco de paredes em lajes de concreto pode ser feito de forma não só a deixá-las visíveis, mas também a destacar suas juntas e pontos de fixação, a destacar pequenas cavidades na superfície, que, em geral, estão fabricando defeitos.
- Além disso, o reboco de uma parede de concreto não pode ser feito de forma alguma - a superfície do concreto é simplesmente recoberta com uma impregnação protetora e, como na foto acima, fica à vista como um destaque. Este design é típico de interiores em estilo loft, bem como de estilos modernos, de alta tecnologia, industriais e techno.
- As superfícies ficam totalmente inacabadas ou em fragmentos, dando ênfase a apenas uma parede. Combina bem com alvenaria, painéis de madeira lisa - e até com o mesmo gesso. Esse projeto geralmente envolve não apenas paredes, mas também tetos - especialmente porque em apartamentos, chalés e moradias (veja), eles quase sempre são de concreto.
- Tudo depende do conceito de estilo que serviu de base para a concepção da divisão - portanto, a decisão de rebocar ou não cabe ao proprietário. Não impomos de forma alguma a nossa opinião - apenas informamos o leitor sobre as novas tendências da moda, que, como no caso do vestuário, é mutável, embora baseada em regras imutáveis.
Para quem gosta de acabamentos tradicionais, será útil assistir ao vídeo deste artigo intitulado: “Como rebocar paredes de concreto”. No próprio artigo, você também aprenderá muitas outras informações úteis.
Gesso para concreto
Muitas pessoas estão interessadas em saber como é feito o gesso de concreto GOST e quais requisitos para sua aplicação são impostos pelos padrões atuais. Pois bem, vejamos os principais tipos de argamassas utilizadas para nivelamento e decoração de superfícies de concreto.
- O reboco no interior de instalações residenciais é realizado principalmente com gesso (ver) ou misturas de gesso-cal, uma vez que cor branca simplifica muito o processo acabamento decorativo. Antes de rebocar uma parede de concreto, deve-se avaliar seu estado original e, consequentemente, selecionar o material de nivelamento adequado.
- Em comparação com a alvenaria, as paredes de concreto são sempre mais lisas - pelo menos quando são construídas com painéis pré-fabricados de concreto armado de grande formato. Portanto, ao prepará-los para posterior acabamento, na maioria das vezes você pode dispensar o uso da composição de base, mas utilizá-la imediatamente.
Nas misturas base, ou como também são chamadas, misturas iniciais, as cargas apresentam maior dispersão, o que permite reparar defeitos mais significativos. Estes incluem diferenças nos planos de duas lajes adjacentes, o que é mais típico para tetos, juntas entre painéis, buracos, bem como fissuras no concreto com abertura superior a 2 mm.
Misturas de concreto de areia
Para reparar defeitos tão significativos, melhor material do que concreto arenoso, você simplesmente não consegue encontrá-lo. Trata-se de uma mistura de construção seca composta por cimento Portland, areia fracionada lavada e aditivos que regulam a plasticidade da solução e o tempo de endurecimento da betonilha. Na maioria das vezes, a cal carbonatada é usada como aditivo para misturas de gesso.
Observação! Dependendo da marca do cimento e do tamanho da areia, a argamassa acabada possui diferentes especificações, podendo ser das marcas M150, M200 e M300. Em geral, as misturas de areia e concreto são convencionalmente divididas em três subgrupos: com frações de carga fina, média e grossa. Para misturar soluções de gesso, é necessária uma mistura de grão fino, em que a fração de areia não ultrapasse 1 mm.
- Em princípio, para nivelar a superfície de uma parede de concreto, é suficiente a resistência da betonilha correspondente ao grau M150. Mas ao rebocar algumas estruturas, cuja resistência está sujeita a requisitos particularmente rigorosos, o concreto arenoso M300 também pode ser usado.
Na construção privada, essas misturas são mais frequentemente utilizadas para rebocar paredes de caves (ver) e fachadas. No interior da casa faz sentido rebocar as paredes com concreto arenoso onde a superfície precisa ser nivelada para revestimento com materiais pesados: ladrilhos de grande formato, Pedra natural, fibrocimento ou painéis cerâmicos com cola.
Emplastros quentes
Ao falar sobre o que e como rebocar paredes de concreto, não podemos ignorar as opções de rebocos quentes. Também são misturas secas, apenas em sua composição, em vez de areia, são utilizados enchimentos leves e porosos.
Na maioria das vezes, são adicionados grânulos de vermiculita expandida, esferas de espuma de vidro, perlita e espuma de poliestireno. O filler ocupa mais da metade do volume total das misturas, garantindo assim as propriedades de isolamento térmico do material.
- Cimento branco ou cal são usados como aglutinantes nessas composições - ou ambos. As suas formulações são pensadas ao mais ínfimo pormenor: para além dos componentes principais, contêm também diversos aditivos que garantem a permeabilidade ao vapor da betonilha, as propriedades hidrorrepelentes e a plasticidade da solução.
- Na maioria das vezes, o gesso quente é usado como método auxiliar de isolamento de paredes e é aplicado não na base, mas em uma superfície já isolada com material de laje. Esse gesso também ajudará nos casos em que não seja possível utilizar outros tipos de isolamento.
- A propósito, as propriedades de isolamento térmico de uma betonilha com 5 cm de espessura correspondem às propriedades de uma camada de espuma de poliestireno da mesma espessura. Esta é uma vantagem indiscutível deste material, mas não menos importância é dada à decoratividade da betonilha acabada, que, devido ao grande enchimento, apresenta uma interessante textura granular.
- É por isso que os enchimentos granulares estão incluídos em muitos tipos de rebocos decorativos: tanto para fachadas como para interiores - e podem estar não só secos, mas também prontos a usar. Ao utilizar misturas granulares, rebocar paredes de concreto com as próprias mãos torna-se um puro prazer, já que não há necessidade de realizar algumas operações tecnológicas.
- No reboco da superfície, a argamassa é nivelada com espátula e pronto. Não é necessário alisar e lixar a superfície da betonilha, como se faz no reboco com misturas de gesso, pois a granulometria esconde perfeitamente todos os pequenos defeitos da base de base.
- Para torná-la mais decorativa, uma parede rebocada com gesso quente é simplesmente pintada com tinta permeável ao vapor. Assim, a facilidade de aplicação da mistura na superfície a ser acabada também pode ser considerada uma das qualidades positivas do material.
Mas a vantagem mais importante dos emplastros quentes é a capacidade de passar o vapor através de si mesmos. É esta qualidade que os torna uma opção ideal para paredes construídas em concreto celular: concreto aerado, concreto aerado silicatado e concreto espumoso, a partir dos quais hoje é construída a grande maioria das casas particulares.
Imitação de textura de concreto
No início do artigo foi dito que alguns estilos modernos design de interiores, pressupõe a presença de superfícies sem reboco. Gostaríamos de esclarecer que estes estilos devem corresponder ao ambiente como um todo.
Por exemplo, o design em estilo loft, que deu origem a esta tendência, é utilizado principalmente para casas espaçosas de dois níveis ou grandes estúdios.
- Lá, paredes ou tetos sem reboco parecem bastante harmoniosos, o que é equilibrado por pisos caros, móveis luxuosos, lustres e tecidos. Em quartos standard de área pequena, com pé-direito inferior a 2,8 m, isso não ficará bem.
- Portanto, é melhor rebocar uma parede ou teto de concreto, que você deverá admirar de perto. Isto também é necessário do ponto de vista do conforto da divisão, porque mesmo uma simples betonilha tem certas propriedades de isolamento térmico e também melhora a acústica.
- Que seja um gesso que imite o mesmo concreto, mas você pode colocar nele o desenho que quiser. No processo de acabamento de paredes ou tetos, você pode suavizar todos os defeitos da superfície do concreto ou, ao contrário, enfatizá-los. Você pode borrifar, cobrir a parede com madrepérola - o que seu coração desejar.
O papel principal nessa decoração é desempenhado pela cor cinza com uma grande variedade de tonalidades. É neutro e combina bem com quase qualquer outra cor.
É por isso que a textura do concreto se tornou tão popular! Sua cor se deve à cor do cimento cinza, e para refinar uma parede de concreto existente não é necessário melhor maneira, como usar gesso à base de microcimento.
Técnica de gesso
Na verdade, não há dificuldades especiais aqui em comparação com o reboco convencional. Pelo contrário: durante o processo de preparação, apenas são reparadas imperfeições superficiais significativas: juntas, fissuras, buracos. Pequenos defeitos na forma de cascas e pequenas lascas podem ser deixados intactos, pois participarão do projeto.
Então:
- O principal é que não haja manchas de fuligem, ferrugem, óleo ou mofo no concreto! Isso é importante porque é impossível encobri-los - depois de um tempo eles saem. Você pode encontrar facilmente recomendações para remover manchas de uma origem ou de outra na Internet. Se tudo estiver bem, basta retirar o pó da superfície do concreto e saturá-lo com o contato do concreto.
- Após a secagem da impregnação, pode-se aplicar o gesso. Se você adquiriu a opção de imitar a textura do concreto, provavelmente ela estará pronta para uso e já tingida de cinza. Porém, é possível criar um revestimento com textura semelhante ao concreto usando qualquer gesso texturizado.
- Geralmente são vendidos na cor branca, o que lhe dá a oportunidade de dar asas à imaginação e colorir a mistura a seu critério. Antes de fazer qualquer textura na superfície, aplica-se primeiro a primeira camada de gesso, tingida de acordo com o fundo principal da imagem.
- É aplicado sobre a superfície preparada com espátula veneziana, cuidadosamente alisada e a seguir, enquanto a camada mantém sua plasticidade, é processada mecanicamente. Para isso, utilize uma escova metálica “1000 linhas”, ou outra ferramenta improvisada, com a qual poderá fazer pequenas conchas na betonilha.
- Agora é necessário dar um pouco de tempo para o gesso endurecer, após o qual a camada estruturada é compactada com a mesma espátula. Conchas quase imperceptíveis permanecem na superfície - quase exatamente as mesmas que no concreto real. Após cerca de seis horas, você pode começar a decorar diretamente a superfície.
- Primeiramente é retirada a cera veneziana transparente que, depois de diluída 1:1 com água, é aplicada com pincel maclave na parede rebocada. Ele secará em duas horas. A próxima camada será colorida, também cinza. Também é aplicado com pincel, depois esfregado bem com uma esponja e deixado secar. Agora você pode formar diretamente o padrão concreto.
- Podem ser listras, gotas, manchas, respingos - o que sua imaginação permitir. O material decorativo é tingido com uma cor mais saturada e aplicado em listras estreitas com uma esponja comum. Usando uma esponja grande e de poros grandes, essa tira é sombreada, criando efeitos de envelhecimento ou desgaste. Após o acabamento do fragmento, ele é polido com leve pressão e movimentos prolongados da espátula.
- Essa decoração pode ser feita não apenas em painéis de concreto, mas também em alvenaria de blocos. Além disso, no reboco, as juntas entre os blocos não são cobertas, mas ficam visíveis. Você pode seguir outro caminho. Se a superfície de base apresentar muitas irregularidades que exijam a aplicação de uma espessa camada de gesso, é mais fácil cobri-la com gesso cartonado e depois decorar sua superfície como concreto.
Muitos, aliás, fazem exatamente isso, destacando as juntas entre as telhas, fazendo furos redondos ou quadrados nelas, simulando fixações. Ao mesmo tempo, a parede ou o teto parece uma folha forrada e parece que é montado a partir de lajes de concreto lisas e de pequeno formato.
Hoje, um método original e barato de acabamento de fachadas e superfícies de paredes internas é popular - gesso decorativo para parecer concreto. A mistura de gesso acabada difere da usual: contém pequenos seixos e grandes grãos de areia, que brilham aos raios de luz e refletem com um brilho perolado.
À venda estão misturas de diferentes tonalidades: cinza, bege, azul, amarelado, marrom claro, verde claro e outros. Você pode dar ao gesso cinza com aparência de concreto a tonalidade desejada de forma independente, adicionando um pouco de tinta acrílica.
Vantagens do gesso decorativo para concreto aplicado por você mesmo.
A aplicação correta, a imaginação demonstrada com habilidade e moderação, a compatibilidade com outros elementos da estrutura são a chave para que o gesso não fique pior do que ladrilhos caros. Este revestimento tem outras vantagens:
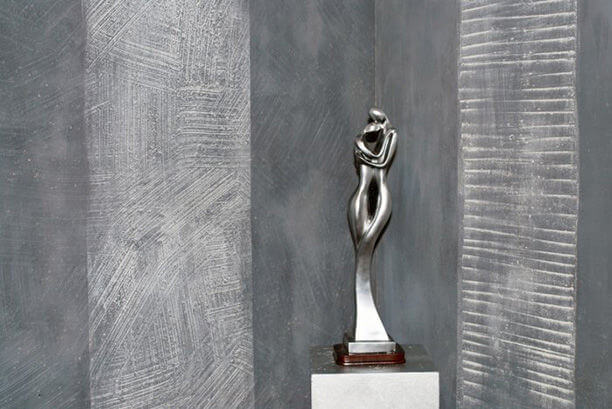
Características de trabalhar com a mistura acabada.
O gesso decorativo para concreto não possui uma estrutura sólida, mas sim porosa. Cubra a parede em várias camadas. Isso consegue o efeito de uma superfície em relevo e volumétrica. Existem mais de 10 opções de aplicativos no total, mas consideraremos apenas as mais populares.
Dica: O gesso translúcido ajudará a criar um efeito impressionante. Esta parede fica especialmente interessante com iluminação decorativa.
Um revestimento nobre será obtido se utilizar uma composição intercalada com a cor dourada. Uma parede de concreto dourado é inesperada e elegante. Existem misturas com outros efeitos: ferrugem, desgaste, prata, bronze, concreto com eflorescência, concreto artístico, etc. O gesso de concreto barato está disponível principalmente na cor cinza, mas você pode adicionar um pigmento colorido para obter a tonalidade desejada. Se você for experimentar cores, lembre-se de que precisará de uma máquina de tingimento.
Fabricantes de misturas de gesso.
Aqui estão algumas das empresas que vale a pena considerar:
- Os produtos da empresa russa Prof Decor incluem uma variedade de gesso para interiores em estilos loft, minimalista e de alta tecnologia.
- A empresa produz peças decorativas misturas de gesso baseado em polímeros. Esses revestimentos são fortes, duráveis, resistentes à umidade e adequados para acabamento de superfícies curvas.
- A empresa Krasnodar Asti produz composições de concreto texturizadas Hi-teck com boa capacidade de economia de calor. As misturas contêm inclusões para criar efeitos diferentes.
- Os produtos Flex Beton System são gessos destinados a superfícies expostas ao calor ou em contato com umidade.
Procedimento de operação.
Primeiro você precisa remover o revestimento antigo da parede. O reboco existente, que não adere bem e já começou a esfarelar, pode ser limpo com uma espátula, depois de humedecer a parede com água. Deixe a água penetrar na camada de gesso para amolecê-la, após o que o revestimento sairá facilmente se raspado. Deve-se ter cuidado especial para remover qualquer reboco remanescente de cavidades e juntas.
Se a parede foi revestida com papel de parede, eles são removidos da mesma forma. É mais difícil, mas esse trabalho pode ser feito. Compre um composto especial que dissolva tinta velha em uma loja de ferragens ou mercado. Um pequeno frasco é suficiente para vários metros quadrados.
Importante: a composição é tóxica, por isso use luvas, respirador e trabalhe em local bem ventilado.
Primário.
Uma parede seca, sem gesso, papel de parede ou tinta, deve ser preparada. Graças a este procedimento simples, o reboco de concreto acabado com as próprias mãos parecerá ter sido aplicado por um profissional. O primer garante boa aderência da mistura à superfície, e o antisséptico também protege o material do aparecimento de mofo e bolor.
Dica: se houver vestígios de mofo na parede, trate com um composto antibacteriano.
Use a composição do primer sem diluição, salvo indicação em contrário nas instruções. Ao diluir com água, certifique-se de que a consistência seja uniforme. Aplique o primer com pincel largo. Um rolo de espuma não é tão conveniente porque o primer escorre muito (do pincel também, mas menos). Aplique a primeira demão, espere secar e depois aplique novamente. Na segunda vez, o primer será aplicado melhor do que na primeira vez.
Aplicação de pseudo-concreto.
A parede preparada é coberta com um substrato - uma mistura de tinta e areia. O gesso decorativo semelhante a concreto do tipo "faça você mesmo" é aplicado melhor e de maneira mais uniforme em tal “almofada”. Posteriormente, ele segura com mais firmeza, não racha nem deforma. É melhor comprar a composição pronta, pois é feita com tinta especial e alguns componentes são adicionados para conferir propriedades antibacterianas e melhorar a adesão.
Pense com antecedência que tipo de textura de superfície você deseja obter. Ferramentas de aplicação:
- espátulas de diferentes larguras;
- Mestre, tudo bem;
- escovar;
- varinha.
Para criar um relevo complexo, é útil um rolo coberto com uma malha de metal. Você pode usar outros dispositivos, dependendo da sua ideia. Exatamente como aplicar deve estar escrito na embalagem do gesso decorativo de concreto. Há uma coisa regra geral: quanto mais complexo o padrão, mais finas são as camadas e maior é o seu número.
Métodos de aplicação populares.
- Usar uma vassoura é uma opção simples e acessível que não requer habilidades especiais. Mergulhe a ponta da vassoura na mistura preparada e borrife na parede, batendo nas hastes com algum objeto. O resultado é um revestimento original e bonito.
- Se o método anterior parecer muito simples, tente sombrear. Use uma escova de aço para escovar a superfície: ficará assim desenho gráfico. Escolha experimentalmente a direção dos traços.
- Usando estênceis prontos. O método será útil para quem tem medo de não conseguir aplicar lindamente o gesso sob o concreto. Os estênceis facilitam a tarefa: com eles o desenho dado é obtido por si só.
- Mistura de gesso de cores diferentes. Você se considera um artesão experiente? Então esta opção é certa para você.
Conselho: se você nunca trabalhou com gesso decorativo para concreto, primeiro pegue um pedaço de compensado ou fibra e experimente trabalhar nele. Quando tiver certeza de que o material “ouve” você, comece a rebocar a parede.
O tempo de pega do reboco de concreto é de aproximadamente 20 minutos, podendo haver desvios em uma direção ou outra. Após este tempo, alise a superfície com uma espátula. Depois de uma hora, retoque com lixa. Isso permitirá que você obtenha um desenho mais preciso e expressivo. A secagem completa ocorrerá após 24 horas.
Assista ao vídeo mostrando como aplicar corretamente gesso decorativo para concreto:
Como deixar o revestimento ainda mais impressionante?
Você pode envernizar o gesso, então ficará nobre e incomum. Também está à venda uma cera especial - também adequada para acabamento. Se você quiser que a parede brilhe e brilhe à luz do dia ou artificial, cubra-a com gesso.
Quanto custa e onde comprar?
Maneiras confiáveis de comprar gesso para concreto cinza são por meio de intermediários oficiais que trabalham com fabricantes e em lojas de materiais de construção conhecidas. As chances de comprar produtos de baixa qualidade de vendedores “nomeados” são reduzidas a zero. Você também pode encomendar gesso decorativo para acabamento de concreto em uma loja online especializada.
Como calcular o custo?
O preço do gesso de concreto faça você mesmo depende do material com o qual você trabalhará. Se for escolhida uma imitação regular de concreto, o custo por 1 m2 será de 600 a 800 rublos. O mesmo se aplica a materiais com efeito de superfície envelhecido. Um revestimento simples com inclusões decorativas custará 1.000 rublos. por metro quadrado m. Se você precisa de uma opção mais exclusiva, e não apenas do efeito de uma parede de concreto, prepare-se para desembolsar o equivalente a 1.300 rublos. por metro quadrado. Os custos finais dependem do consumo de material.
Leia também:
Reboco do porão de uma casa: fotos e vídeos
Os principais tipos de paredes de concreto na construção de edifícios baixos e de vários andares são estruturas de concreto leve e pesado. A vida útil e o conforto da edificação dependerão da escolha do material. As paredes de concreto leve (espuma) são feitas de concreto aerado, concreto espumoso ou concreto espumado a gás, obtido pela adição de aditivos especiais à base de cimento.
Blocos para paredes de concreto pesado e as vantagens dos blocos de concreto
O que é um bloco de concreto?
Os blocos de concreto são chamados de materiais de parede feitos de concreto pesado. Os blocos de concreto para paredes são caracterizados por alta capacidade de carga, mas ao mesmo tempo baixas propriedades de isolamento térmico e acústico. Quando a alvenaria é feita de pedras de concreto com vazios, é possível reforçar a estrutura da parede com reforço através dos vazios das pedras. Após a instalação da armadura, os vazios são preenchidos, ou seja, neste caso os blocos desempenham um papel cofragem permanente. As pedras faciais podem ser produzidas em diversas cores (com introdução de pigmento no processo produtivo), além de diversas texturas.
O que é concreto como material de parede?
O concreto é um dos principais materiais utilizados na construção. A vantagem da utilização do concreto para produtos de construção, do ponto de vista técnico e econômico, é a utilização de materiais locais e, consequentemente, a redução dos custos de produção e fabricação.
Quais são as vantagens dos blocos de concreto na construção de paredes?
O concreto é durável e resistente ao fogo; Dependendo das condições de uso exigidas, suas características como resistência e densidade podem ser variadas. Com base na densidade, os concretos são divididos em: extra pesado (densidade superior a 2.500 kg/m2), pesado (2.200-2.500 kg/m2), leve (1.800-2.200 kg/m2), leve (500-1.800 kg/m2) e extra leve (menos de 500 kg/m2). m2). A partir da mistura de concreto, com processamento adequado, é possível produzir produtos com o formato desejado, incluindo blocos de parede - maciços e vazados, aparentes e comuns. Além disso, as pedras em blocos de concreto pesado endurecem em condições naturais, durante a vaporização ou como resultado do tratamento em autoclave.
Paredes de casas feitas de concreto leve
O que são tipos leves de concreto?
Paredes feitas de concreto leve (espuma) retêm quase todas as vantagens alvenaria. Os blocos de espuma de concreto são feitos de cimento, areia, água e agente espumante. São utilizados principalmente agentes espumantes sintéticos à base de compostos orgânicos. Aditivos de solução de cola animal, sulfato de ferro, vidro líquido. O alto teor de ar na forma de minúsculos poros torna o material um bom isolante térmico. O tamanho relativamente pequeno dos blocos e a facilidade de processamento tornam possível construir paredes de configurações complexas a partir deles. Na construção de moradias baixas, blocos de espuma de concreto de grau 500 e superior são usados como estruturas de parede de suporte. Via de regra, blocos de grau 400 são usados como isolamento térmico. A espessura das paredes de concreto espumoso pode ser metade da espessura das paredes de tijolo. Revestir a parte externa das paredes de espuma de concreto com tijolos decorativos não aumenta significativamente seu peso, mas fortalece a estrutura e elimina preocupações com o acabamento.
Os blocos de espuma de concreto para paredes são feitos de cimento, areia, água e agente espumante. Os produtos distinguem-se pelas boas propriedades de isolamento acústico e térmico e pelo baixo peso. O material não é inflamável e não entra em colapso devido à exposição Temperatura alta. As propriedades do concreto espumoso são grandemente influenciadas pela qualidade do agente espumante. Atualmente, são utilizados principalmente agentes espumantes sintéticos à base de compostos orgânicos, nacionais e importados. Aditivos de uma solução de cola animal, sulfato de ferro e vidro líquido são usados como estabilizadores de espuma; Os ligantes são cimento e cal. Na construção de moradias baixas, os graus de concreto espumoso de D500 e superiores são usados como estruturas de suporte das paredes da casa. Via de regra, os blocos da marca D400 são utilizados como isolamento térmico. Fazer espuma de concreto (especialmente sem autoclave) é uma operação bastante simples, por isso existem fabricantes do material em quase todas as regiões da Rússia.
Propriedades dos blocos de espuma de concreto, suas vantagens e aplicações
Quais são as propriedades físicas e mecânicas do concreto espumoso?
Blocos de espuma de concreto podem ser serrados, perfurados e fresados. Os elementos de acabamento das paredes acabadas são fixados com pregos, como acontece com a madeira comum. Em termos de características e propriedades de consumo, os blocos de espuma de concreto estão mais próximos da madeira, mas apresentam maior durabilidade. O concreto espumoso é muito fácil de instalar, pois os blocos têm um tamanho bastante grande, apesar de serem leves. Por exemplo, um bloco medindo 600x300x250 mm não pesa mais que 18 kg, o que pode reduzir significativamente os custos de mão de obra. Uma equipe de 3 pessoas pode montar uma casa de blocos de espuma com área de 120 m2 em apenas 10 a 12 dias úteis.
Quais são as vantagens dos blocos de espuma de concreto e as paredes de espuma de concreto são capazes de armazenar calor em uma casa?
Em termos de qualidades de isolamento térmico, 30 cm de espuma de concreto equivalem a 75-90 cm de concreto de argila expandida ou 150-180 cm de tijolo. E como o calor não atravessa as paredes da casa, mesmo a utilização de sistemas de aquecimento eléctrico não afectará o orçamento do proprietário.
Onde é melhor usar espuma de concreto?
O concreto espumoso absorve prontamente a umidade. Paredes de concreto leve não toleram deformações, por isso requerem durabilidade Fundação tira ou fundação em laje. Deve passar um ano entre a conclusão do assentamento da parede e o início do acabamento, para que as paredes possam “assentar”. Lajes de concreto não podem ser utilizadas. O concreto leve ocupa uma posição intermediária entre o tijolo e a madeira, e quanto mais alto é Gravidade Específica, mais próximas suas propriedades estão do tijolo. A utilização de blocos de espuma de concreto é aconselhável na construção de pequenas casas (não mais de 2 andares) e dachas destinadas ao uso durante todo o ano.
Vantagens das paredes feitas de blocos de concreto aerado
O concreto aerado em suas qualidades estruturais é fundamentalmente diferente de todos os outros materiais de parede. As vantagens dos blocos de concreto aerado são que esse material pode reduzir significativamente o peso e a espessura das paredes, o que não só reduz o custo da obra devido à economia na construção de fundações, mas também reduz o tempo e o volume de construção.
Estruturas de parede feitas de concreto aerado possuem altas propriedades termofísicas em comparação com blocos feitos de concreto pesado, tijolos cerâmicos e de silicato. Por exemplo, para um dispositivo parede externa Blocos de concreto poroso com espessura de 375 mm (densidade 400 kg/m2) são adequados. O concreto aerado tem a capacidade de absorver a umidade do ar quando a umidade interna é alta e devolvê-la quando diminui. Os blocos de concreto aerado possuem dimensões geométricas precisas (tolerâncias +1 mm) e uma superfície lisa. Isto permite a colocação das paredes de uma casa em betão celular com uma cola mineral especial, que evita a formação de “pontes frias” que ocorrem no assentamento de blocos sobre a habitual argamassa de cimento-areia. Os blocos de parede são produzidos em dois tipos, lisos e macho-fêmea, o que facilita muito o trabalho. Além de blocos de parede, coberturas e lajes podem ser feitas de concreto aerado, Painéis de parede, saltadores, etc.
Blocos de concreto aerado são usados: na construção de paredes combinadas em edifícios de vários pisos, na construção de edifícios residenciais baixos (até 3 pisos), e também como isolamento. Além disso, os blocos de concreto aerado são fáceis de processar, não corroem e não apodrecem. Os trabalhos de instalação de paredes em blocos de concreto aerado são realizados em temperaturas de até 0°C; ao usar cola resistente ao gelo até -5°C.
Fachada em estuque. Ordem decoração de fachada em concreto armado com fibra de vidro da produção.